Logiche di gestione
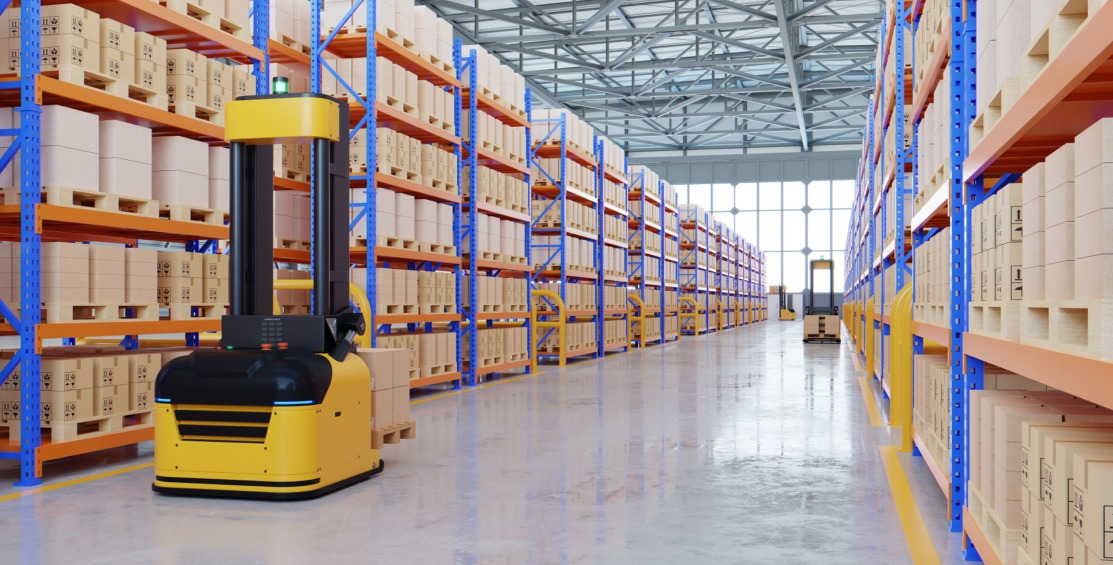
Magazzino automatizzato – missioni AGV
Una realtà industriale, attiva nel campo della produzione di carrelli a guida automatica AGV, ci ha chiesto una collaborazione per automatizzare
la logistica di un birrificio di levatura internazionale della Catalogna.
Il sistema di movimentazione del magazzino prevedeva l’utilizzo in contemporanea di 10 nuovi veicoli a guida automatica AGV, più alcuni carrelli
di scorta che si dovevano attivare automaticamente in caso di guasto o sosta per la ricarica delle batterie di uno dei 10 mezzi titolari.
La movimentazione era prevista h24 e aveva come obiettivo primario l’abbattimento dei tempi di consegna degli ordinativi, l’integrazione con il sistema
di produzione aziendale nonché la riduzione dei costi di handling.
Il sistema di stoccaggio e movimentazione delle merci in essere era stato giudicato insoddisfacente e troppo lento in quanto non riusciva a garantire
le consegne degli ordinativi nei tempi richiesti dal mercato.
L’azienda fornitrice dei carrelli AGV aveva quindi la necessità di un supporto per progettare le logiche di gestione del magazzino. Dopo aver posizionato
le linee guida magnetiche all’interno degli spazi fisici di stoccaggio, programmato la comunicazione tra il PLC del carrello e le linee guida, definito
le micro-tratte, era necessario assegnare ad ogni veicolo la missione corretta ossia dire quale bancale di birra caricare, dove posizionarlo e comporre
le micro-tratte per definire il tragitto completo da compiere.
Per assegnare le missioni bisognava tenere in considerazione determinati vincoli:
- Lo scarico/carico dell’autotreno in arrivo presso la baia di carico avveniva in maniera automatizzata, in un’unica operazione: i vani di carico degli
automezzi erano stati modificati appositamente per permettere lo scarico dei vuoti resi e il carico delle palette da consegnare in un’unica manovra,
così da tenere il mezzo fermo il minor tempo possibile. Ciò comportava la necessità che la missione degli AGV fosse programmata per preparare la baia
con la merce necessaria ad una sola movimentazione della pala e non con più riempimenti successivi dell’autotreno.
- La merce in uscita dal magazzino doveva seguire una logica FIFO (First In First Out)
- Bisognava ottimizzare gli spazi, impilando anche, ove possibile, diversi pallet di merce, tenendo in considerazione che confezioni di prodotto differenti
potevano reggere il peso di pile differenti (es. un pallet di lattine sopportavano un carico differente da confezioni di bottiglie a collo lungo).
- Ogni corsia poteva essere occupata solamente da un carrello, quindi, nel caso di una corsia impegnata in una operazione di carico/scarico, un secondo
carrello doveva seguire un percorso differente.
- Messaggi di allarme: nel caso di un evento imprevisto, il sistema genera dei messaggi di allarme come, ad esempio, la presenza fisica di una persona
lungo il tragitto oppure la posizione non corretta di una colonna di pallet. Nel caso di allarme il veicolo doveva adeguare la missione di conseguenza.
- Su specifica richiesta della committente il protocollo di comunicazione tra carrelli e infrastruttura doveva avvenire a livello TCP, senza l’interfaccia
di librerie.
Per poter gestire la richiesta del cliente in tutte le sue possibili casistiche e con i vincoli specificati, abbiamo deciso di portare la memorizzazione
dei dati, che prima avveniva a livello di PLC, su un database condiviso. Abbiamo valutato che la perdita di velocità nell’accesso al dato non avrebbe
assolutamente compromesso le prestazioni del sistema, data la poca velocità di movimento dei carrelli AVG.
Questo ci ha però permesso di creare una struttura dati accessibile in contemporanea da più macchine e di poter creare una sorta di monitor della situazione
in tempo reale, in modo da poter creare le missioni per i carrelli, impartirle, coordinarle e all’occorrenza modificarle. Il tutto in maniera automatizzata.
Il principio con cui abbiamo sviluppato la soluzione è stata la configurabilità del sistema. La progettazione del software è stata fatta tenendo in
considerazione che la disposizione delle aree fisiche del magazzino possono cambiare nel tempo così come le altre logiche di stoccaggio della merce.
Così facendo non vi è la necessità di riscrivere il programma ad ogni modifica ma solo di cambiarne la configurazione. Quella che deve rimanere immutata
è la logica di funzionamento per cui si è scomposto il macro-problema in tanti micro-task: modificando i parametri di questi ultimi la logica di
funzionamento dell’intero sistema rimane immutata ma diviene parametrizzabile.
Elemento qualificante del team di lavoro è stata la Universidad de la Catalunya. Questa era stata incaricata dall’azienda di beverage di validare
il sistema progettato, prima di essere messo in produzione.
Abbiamo dovuto così coordinarci con un gruppo di lavoro composto dai tecnici di: committente spagnola, azienda tedesca realizzatrice dell’impianto
di birrificazione, impresa di produzione carrelli AGV e dipartimento dell’università.
In particolare, al fine di validare la nostra soluzione, l’Università ci ha messo a disposizione, oltre al ricercatore incaricato, un sistema di
simulazione della linea di produzione. È stato così possibile eseguire una serie di test preventivi sul comportamento delle logiche da noi implementate,
verificando una serie di casistiche corrispondenti a quelli che sarebbero stati mesi di lavoro.
Il risultato, giudicato soddisfacente dall’Università, ci ha così permesso di mettere in produzione senza imprevisti la soluzione sviluppata,
rendendo completamente automatizzata la movimentazione del magazzino, riducendone i costi, i tempi di fermo mezzi e rendendo un flusso continuo
e coordinato il processo ordine, produzione, stoccaggio e consegna.